Revolutionizing Production: The Dynamics of Manufacturing ERP Software
In the intricate landscape of modern manufacturing, where precision, efficiency, and adaptability are paramount, Manufacturing Enterprise Resource Planning (ERP) software emerges as a transformative solution. Tailored to meet the unique challenges of the manufacturing industry, ERP software serves as the backbone of operations, integrating various processes, optimizing resources, and providing a holistic view of the production lifecycle. In this article, we delve into the world of Manufacturing ERP Software, exploring its key functionalities, advantages, and the pivotal role it plays in revolutionizing production processes across diverse manufacturing sectors.
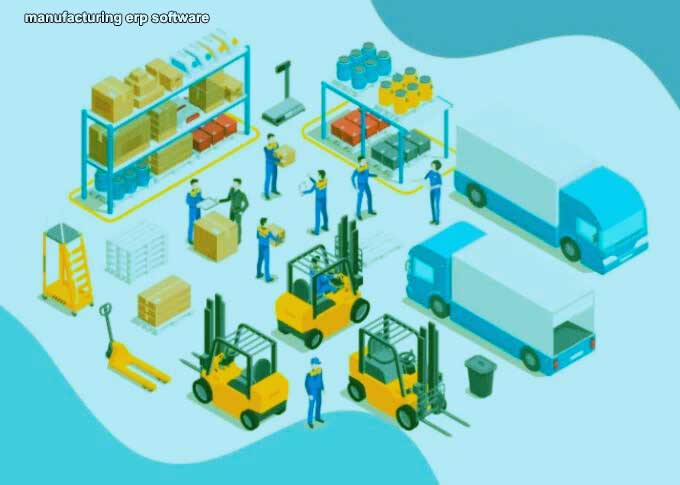
Decoding Manufacturing ERP Software
1. Holistic Integration of Manufacturing Processes: At its core, Manufacturing ERP Software focuses on the holistic integration of diverse manufacturing processes. From order processing and production planning to inventory management and quality control, the software ensures that all facets of the manufacturing operation work seamlessly together. This integration minimizes manual efforts, reduces errors, and enhances overall operational efficiency.
2. Real-Time Production Planning and Scheduling: Efficient production planning and scheduling are critical in manufacturing. Manufacturing ERP Software excels in real-time planning and scheduling, taking into account factors such as machine capacities, resource availability, and order priorities. This optimization minimizes idle time, accelerates production cycles, and ensures timely order fulfillment.
3. Inventory Optimization and Supply Chain Management: Effective inventory management and supply chain optimization are key strengths of Manufacturing ERP Software. The software provides real-time visibility into inventory levels, automates reorder processes, and streamlines supply chain activities. This results in reduced holding costs, minimized stockouts, and a well-balanced and cost-effective supply chain.
Key Functionalities of Manufacturing ERP Software
4. Bill of Materials (BOM) Management: Manufacturing ERP Software incorporates robust Bill of Materials (BOM) management. This detailed list of components and subassemblies required for production ensures accurate material planning, cost estimation, and streamlined production processes.
5. Quality Control and Compliance: Ensuring product quality and compliance with industry standards is paramount in manufacturing. ERP software includes modules for quality control, enabling businesses to monitor and enforce quality standards throughout the production process, from raw materials to the finished product.
6. Shop Floor Control and Machine Integration: Manufacturing ERP Software extends its functionalities to the shop floor, providing shop floor control features and integrating with machines and equipment. This connectivity ensures real-time monitoring of machine performance, production progress, and overall shop floor efficiency.
Advantages of Manufacturing ERP Software
7. Improved Operational Efficiency: Manufacturing ERP Software significantly improves operational efficiency. By automating routine tasks, providing real-time insights, and optimizing production processes, businesses can operate more smoothly, minimize downtime, and adapt quickly to changes in demand.
8. Enhanced Visibility and Decision-Making: Real-time data visibility is a key advantage of Manufacturing ERP Software. Businesses gain insights into production performance, resource utilization, and key performance indicators. This data-driven approach enhances decision-making, enabling businesses to make informed choices for process improvement and cost reduction.
9. Scalability for Growth: Manufacturing ERP Software is designed to scale alongside business growth. As production volumes increase, the software can accommodate additional data, users, and functionalities without compromising performance. This scalability ensures that the software remains effective and aligned with evolving business needs.
Considerations When Implementing Manufacturing ERP Software
10. Integration with Manufacturing Equipment: Effective implementation of Manufacturing ERP Software requires seamless integration with manufacturing equipment and machines. This connectivity ensures real-time monitoring and control, optimizing the use of manufacturing resources.
11. User Training and Adoption: User training is crucial for successful Manufacturing ERP Software implementation. Providing comprehensive training programs ensures that employees can navigate and utilize the full functionalities of the software, maximizing its impact on daily manufacturing operations.
12. Customization to Industry-Specific Needs: Manufacturing ERP Software should be customizable to industry-specific needs. Whether in discrete manufacturing, process manufacturing, or mixed-mode manufacturing, the software should cater to the unique requirements of the industry, ensuring relevance and effectiveness.
The Future of Manufacturing ERP Software
As technology continues to advance, the future of Manufacturing ERP Software holds exciting possibilities. Anticipated trends include increased integration with Internet of Things (IoT) devices for enhanced connectivity, advanced analytics for predictive maintenance, and the continued integration of artificial intelligence to further optimize production processes.
In Conclusion: Redefining Manufacturing Excellence
In conclusion, Manufacturing ERP Software stands as a cornerstone in redefining manufacturing excellence. Its ability to integrate processes, optimize resources, and enhance overall operational efficiency positions it as a strategic asset for manufacturers across diverse industries. As the manufacturing landscape evolves and demands increased agility and adaptability, the adoption of Manufacturing ERP Software becomes not just a technological upgrade but a crucial step toward achieving operational excellence, driving innovation, and sustaining growth in a highly competitive and dynamic manufacturing environment.